12インチ・ダブテールジョイントジグとハーフブラインド・ダブテールジョイント
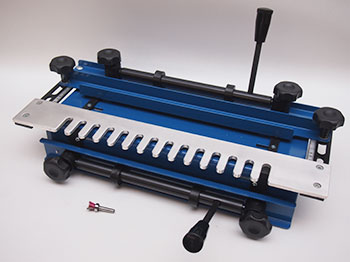
これが12インチ・ダブテールジョイントジグです。
このジグで1インチ(25.4mm)ピッチのハーフブラインド・ダブテールジョイントの加工ができます。
加工できる板は、厚さ15~31.7mm、幅は最大285mm、長さは約20cm以上で、これより短いと上面のリアクランプに固定することができません。
前側のフロントクランプでは板の長さが約12cm以上必要です。
付属の6mm軸のベアリング付き専用ダブテールビットで加工します。トリマでも加工できることがこのジグの大きな特徴です。
★商品の詳細はコチラ
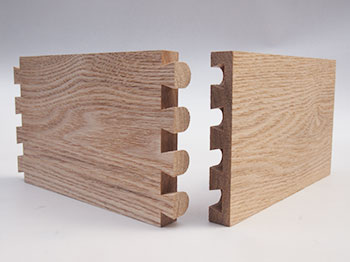
このジグで加工できるハーフブラインド・ダブテールジョイントは、引き出しで例えれば前板になるピンボード(画像右側)と側板になるテールボード(画像左側)で構成され、2枚のジョイント個所を同時に加工します。
シングルパスとかワンパスと呼ばれる方法です。
箱にするには各々2枚必要になります。
ジョイント加工は4回行なうことになります。
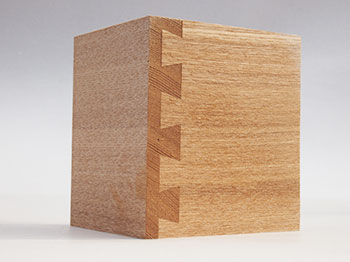
板幅はジグのテンプレートのピッチである1インチ(25.4mm)の整数倍が理想的です。
しかし板幅の制約等で整数倍にできない場合もあると思います。そのような場合は左図のような一方の端がハーフテールの上下が非対称のジョイントになってしまいます。
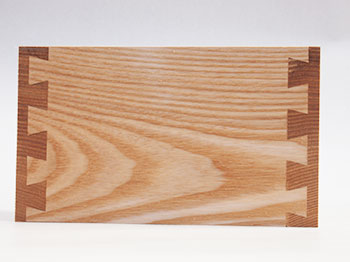
それを通常の方法で加工すると、図のような左右も非対称のジョイントになってしまいます。
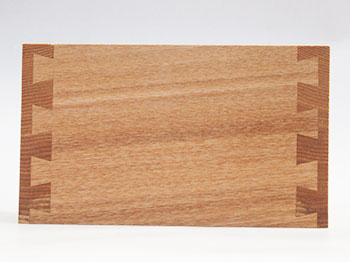
これを左右対称のジョイントにするにはジグ本体右側のクランプも使用します。
上下が対称なジョイントではジグ本体左側のクランプのみの使用でジョイント加工ができます。
六段重ねの箱
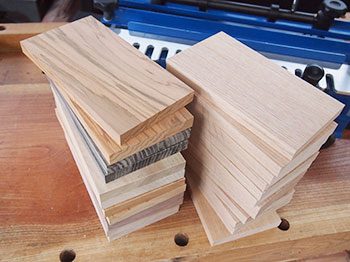
これらが六段重ねの箱に用いる材料です。
ピンボード(引き出しに例えると前板になります)は、サクラ、神代タモ、クス、ケヤキ、ブラックウオールナット、メイプル。
テールボード(引き出しに例えると側板になります)はタモのみです。
ジョイント部のコントラストが明瞭になるよう異なる材料のジョイントにしました。
板の幅は104.2mm、長さはピンボードが200mm、テールボードが188mm、厚さは15.8mm。
テールボードはフロントクランプに、ピンボードはリアクランプにセットします。ここでは上下および左右が対称の箱になるのでジグの左側のみを使用してクランプします。
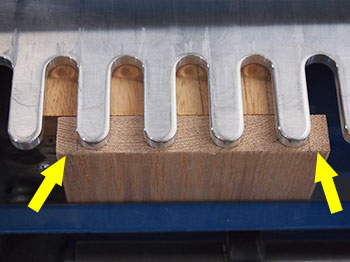
通常、箱の両サイドは強度の面からハーフピンになるようにします。
そのために板幅はテンプレートピッチの25.4mmの整数倍にすることが好ましいのですが、ここではさらに約1.3mm大きなハーフピンになるように25.4mmの4ピッチ分の101.6mm+1.3mmx2の104.2mmにしました。
ジグのサイドストップは約2mmまでハーフピンを大きくさせるようにセットできます。
サイドストップはジョイントの左右が均等になるようにセットします(矢印)。
画像ではセットしやすいように両木端から1.3+6.35=7.65mmの位置の木口面に鉛筆で線を引き、左右が均等になっているかを確認しやすいようにしています。
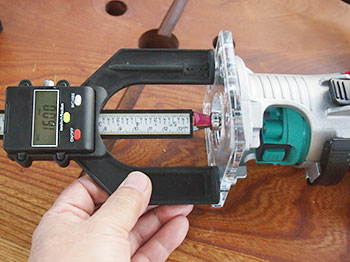
ジグに付属しているベアリング付きのダブテールビットはベースから16mm突き出すようにトリマにセットします。
そして木取りした際の余った材料でテストカットしてジョイントのきつさ加減をチェックします。
固すぎるようであればビットの突出しを少なくし、緩すぎるようであれば多くし、再度テストカットをおこない確認します。
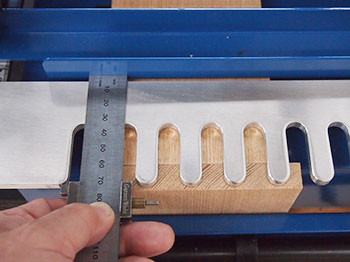
ジョイントの入り具合は、テールボードの板厚が19mmまではフェンスの位置で調整します。
この位置の設定は使用するトリマのベースサイズや板厚等から計算して求めますが、最終的には余った材料でテストカットをおこない、最適な位置に調整します。
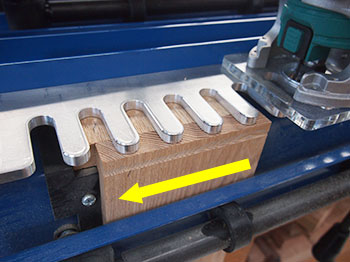
ビットの突出しやフェンスの位置調整のチューニングと合わせて材料の欠けやすさもチェックします。
最初にフロントクランプ側のテールボードをビットの先端で極浅くクライムカットします。
このクライムカットはビットの回転方向と切削方向が同じになるのでコントロールしにくく、トリマを持って行かれる傾向があり危険なテクニックですが、切削部に欠けなどが生じにくいという特徴があります。
しかし、特にベースの小さなトリマではテンプレート上での安定性があまり良くないのでお勧めできません
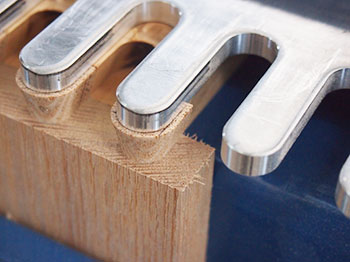
また、クライムカットしても刃先の届かないテールボードの右端の木端にはササクレが生じてしまいます。
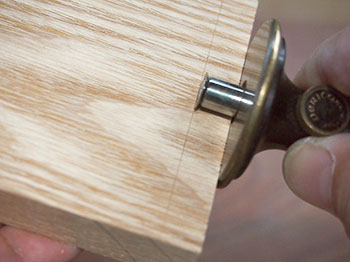
もし、欠けやササクレが多いようでしたら予めビットの切削位置にホイールマーカー等で木の繊維を切断しておくことを推奨します。
また右端は裏側に当て木状にピンボードが位置していなので、テールボードの正面側と右側の木端、その裏側のピンボードが接触しない部分まで表面の繊維を断ち切っておくほうが良いと思います。
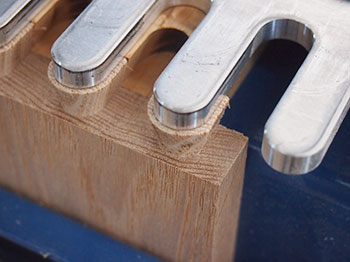
予めホイールマーカー等で木の繊維を断ち切っておくことで右側の木端やその裏側の部分にはササクレは生じませんでした。
ただしその当て木のないテール個所の裏側まで欠けやササクレをなくすことはできません。
これを防ぐには、その個所の裏側にも別途当て木を添える必要があるのかもしれません。
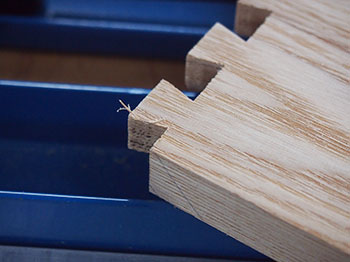
欠けの少ない材料では特に手段を講ずる必要はありません。
またピンボード側も欠けを考慮する必要はないと思います。
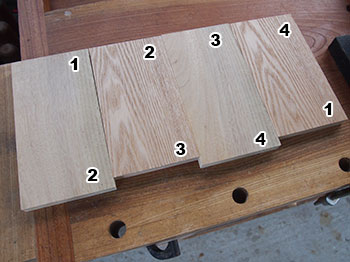
テストカットが終了したら本番。
板の内側になる面にジョイントする際にカップルとなる個所に数字を付けます。
この数字が同じになるようにジグにセットし、同時にカットします。
この一対のジョイントを順を追って加工します。
また、一枚の長い板からこれら四枚の板を切り出し、もとの板の木目の流れを箱にも再現したい場合は、その木目の並び順に番号を付けます。
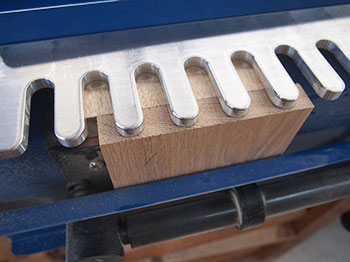
1の数字を付けた板をジグに互いに接するようにセットします。
数字を付けた側が表を向くようにセットします。
リアクランプ側がピンボード、フロントクランプ側のテールボードになります。
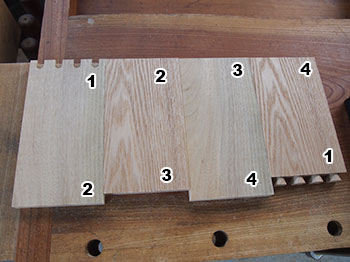
1の数字の位置の加工が終わった状態です。
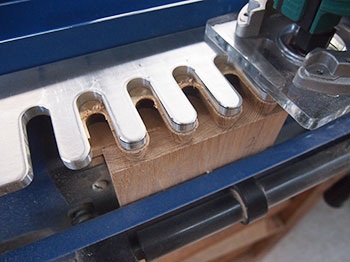
次は2の数字を付けた板をジグに互いに接するようにセットし加工します。
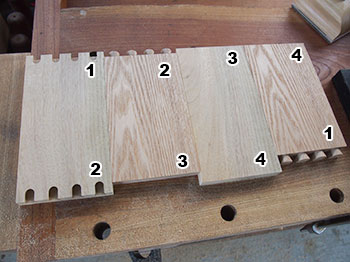
2の数字の位置の加工が終わった状態です。
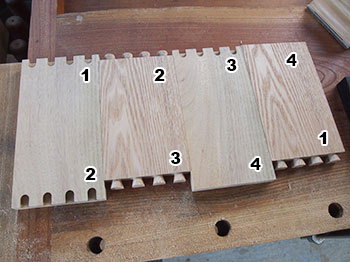
3の数字の位置の加工が終わった状態です。
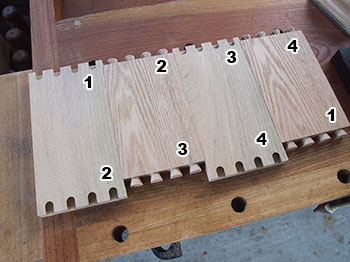
4の数字の位置の加工が終わり、すべてのジョイント加工が済みました。
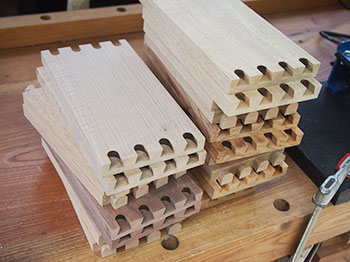
他の材料もジョイント加工。12インチ・ダブテールジョイントジグは一対のジョイント個所をワン・パス(シングルパス)で一度に加工するので迅速な作業が可能です。
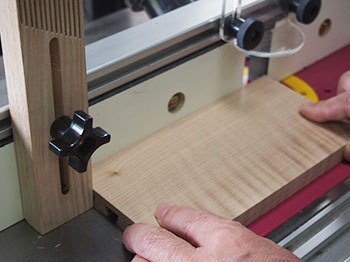
次は厚さ4mmのシナ合板の底板をはめ込むための溝加工。ルーターテーブルを使い、φ4mmのストレートビットで。
溝が外側から見えないよう、途中で止めるためにストッパーで加工位置を制限しています。
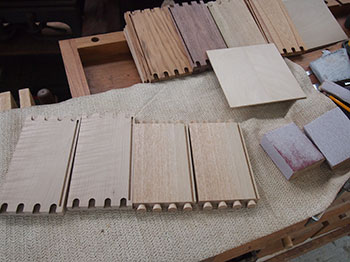
箱の内側になる面や溝をペーパーで仕上げ、
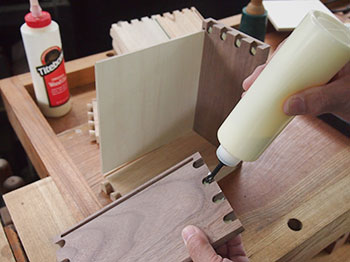
ジョイント部に接着剤を付けて組み立てます。
(底板と溝には接着剤はつけません。差し込むだけです)
最初に側板の1枚をワークベンチ等の上にのせ、対になる番号の前板を差し込み、それらに底板をはめ込みます。
そして側板のもう一方の端と対になる番号の前板を差し込み、最後に残った側板を番号が合うように差し込みジョイントします。
なお、接着個所が狭いので、グルーアプリケーターセット等があると接着剤が塗布しやすくなります。
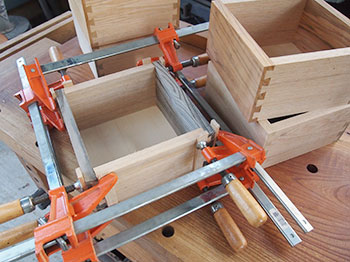
四方からクランプします。
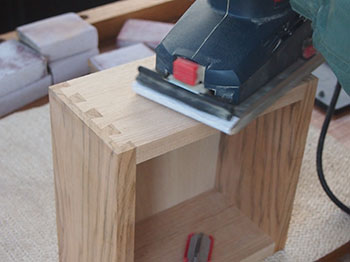
接着剤の硬化後、外側の仕上げ。わずかにピンが飛び出した部分をフラットにします。
この部分は木口ですのではみ出した接着剤が浸み込むと、塗装を弾いてしまいます。
ですから、わずかに木口側が突き出るように加工するのが正解だと思います。
木口側が引っ込んでいるとフラットにするのに広い面を削り落とさなければならず、また浸み込んだ接着剤を除去するのも困難です。
なお、これらのセッティングは事前にフェンスの位置で調整しておきます。
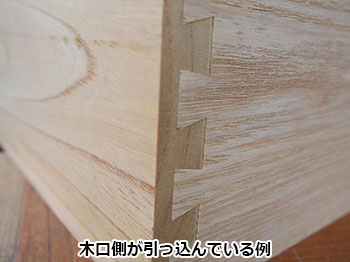
木口側が引っ込んでいる例。
修正するには広い面を削りとる必要があります。
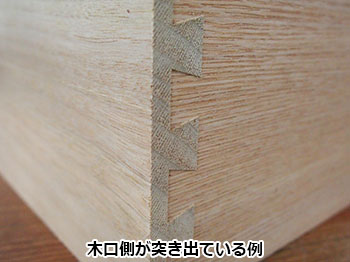
木口側が突き出している例。
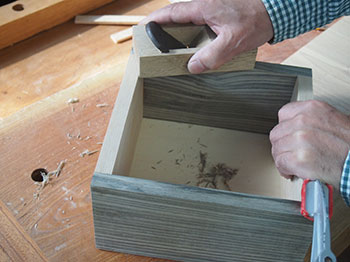
そして目違いをカンナで修正。
なお、この神代タモの箱、後で詳しく説明しますが問題のあった材料。
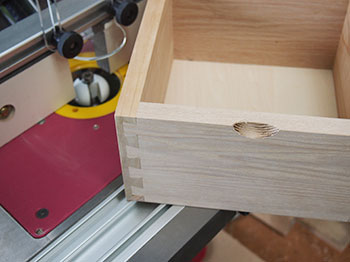
積み重ねたときに指を掛けやすいように側面にサジ面ビットで溝加工。
刃径44.5mmのビットをルーターテーブルで。
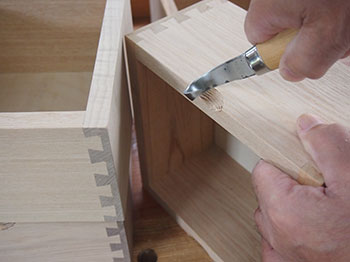
ビットで焦げた個所をフックナイフ等で仕上げ、
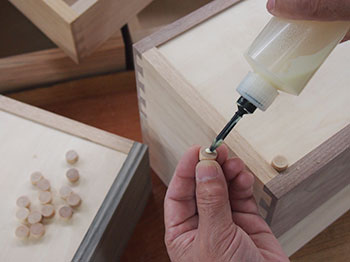
積み上げたときにずれないよう、底板にフラットヘッドの木栓を接着します。
なお、積み重ねたときに一番下側になる箱の底板には大きな荷重がかかることになるので、一番下側になる箱にはこの木栓は付けない方が良いのかもしれません。
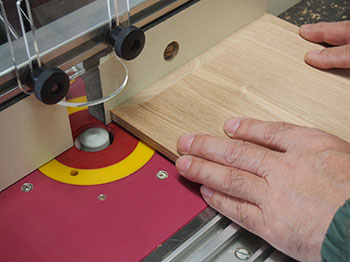
一番上になる箱にはフタをかぶせます。ルーターテーブルを使ってポイントカッティングビットやストレートビットで加工。
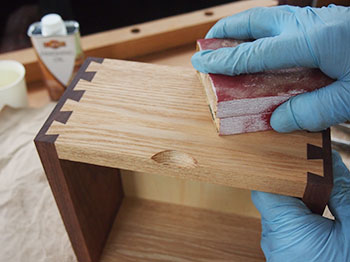
フィニッシングオイルで仕上げ。
オイルが乾かないうちにペーパーで研磨し、切削粉を刷り込みます。
ジョイントの多少のギャップはこの処理でほとんど目立たなくすることができます。
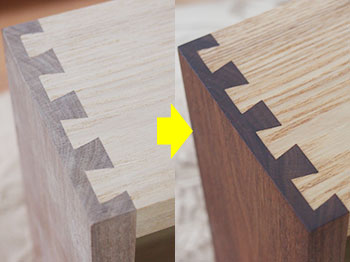
オイルを塗布することでジョイントのコントラストはより鮮明になります、
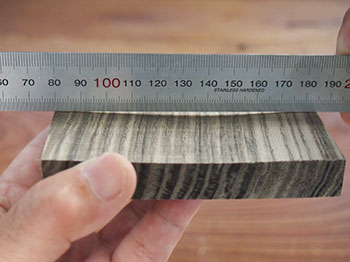
なお、これが問題のあった神代タモ。
大きく反っていました。
でも、貴重な材料なので無駄にしたくないので加熱し矯正し、反りが取れた時点で加工しました。
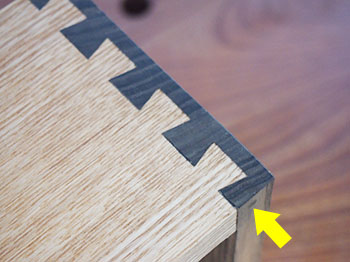
しかし、時間の経過と共に反りが戻ってしまいました。
ジョイントに用いる材料は、均一の厚さ、幅、長さが必要で、各々の面は直角に交差し、反りやねじれのない材料を選定すべきと痛感しました。
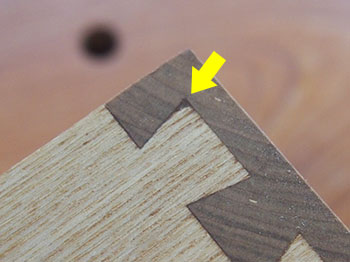
また、欠けが生じ、切削粉を刷り込んでも目立たなくすることができなかった個所は、同じ材料を埋め込み目立たなくしました。

完成した六段重ねの箱。
幅の異なる材料で作る箱
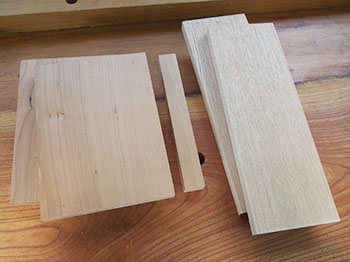
12インチ・ダブテールジョイントジグではピンボードとテールボードの幅が異なっていてもジョイントを加工することができます。
これには2つのポイントがあります。
一つはピンボードと同じ厚さの幅1インチのブロックの使用、もう一つはジグの右側のクランプも使用することです。
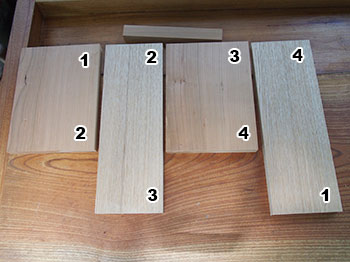
ピンボード(前板)は厚さ18.2mm、幅150mm、長さ200mmのチェリー。
テールボード(側板)は六段重ね箱と同じ15.8mm厚さで、幅104.2mm、長さは300mmのタモ。
6段重ねの箱のつくり方と同じようにそれらの対となるジョイントに番号を付けます。
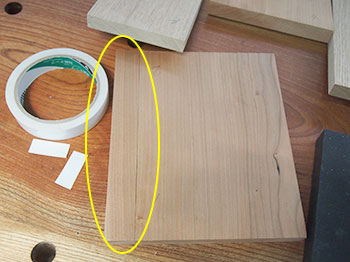
1番目のピンボードの左側に同じ厚さの幅1インチのブロックを貼り付け、サイドストップから材料が丁度1インチ離れてクランプできるようにします。
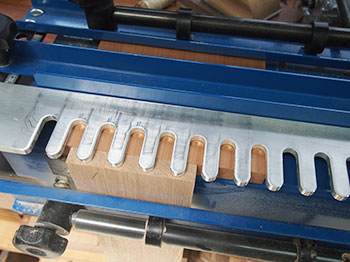
ジグの左側のリアクランプにブロックを貼り付けた1番目のピンボードをクランプし、フロントクランプ側には1番目のテールボードをクランプします。
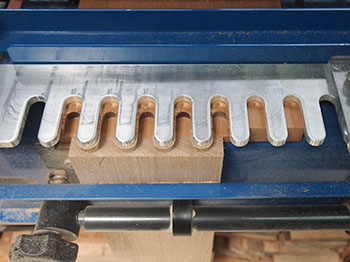
そして専用のダブテールビットでカット。ビットの突出しは六段重ねの箱と同じです。
左側からテールボードに沿ってブロックもカットし、右端を加工した時点で終了とします。
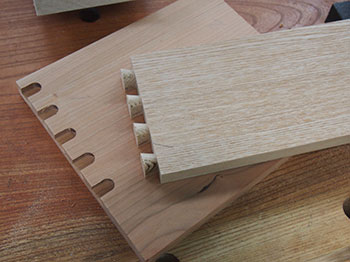
1番目の加工が終了し、ジグから外した状態です。
ブロックはピンボードに付けたままの画像です。
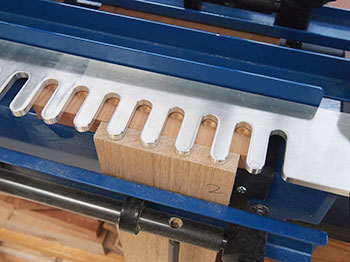
2番目の対となる材料はジグの右側にクランプします。
今度は2番目のピンボードの右側に同じ厚さの幅1インチのブロックを貼り付け、右側のサイドストップから材料が丁度1インチ離れてクランプできるようにします。
なお、右側のサイドストップも左側と同じ大きさのハーフピンになるようにセットしておくことを忘れないでください。
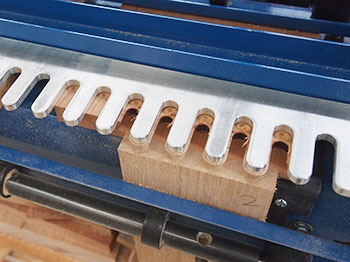
同じように左側からテールボードに沿ってカットし、右端のブロックを加工した時点で終了とします。
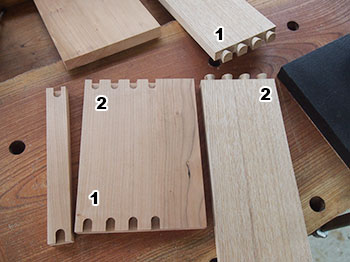
2番目のジョイント加工が終了した状態です。
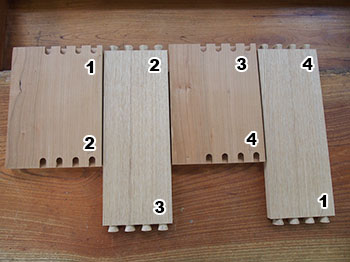
3番目のジョイントの対はジグの左側にクランプし、4番目のジョイントの対はジグの右側にクランプし、すべてのジョイントを加工します。
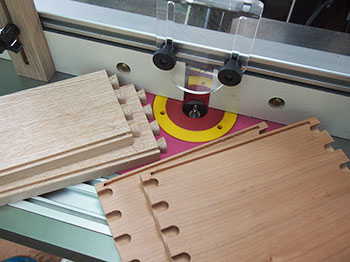
厚さ4mmのシナ合板の底板をはめ込む溝をルーターテーブルを使いφ4mmのビットで加工します。
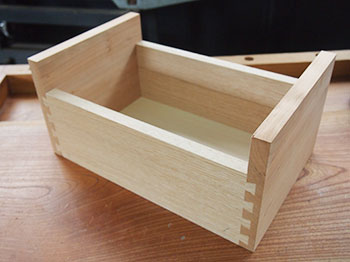
溝の完成時点で仮組みし、キチンとジョイントできているか確認。
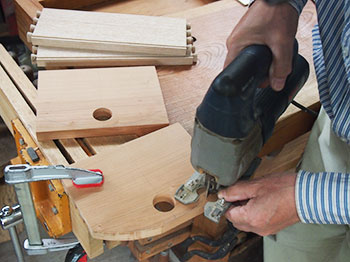
ピンボードは持ち手用のφ30mmの穴をフォスナービットであけ、ジグソーでかまぼこ型のRを付け、
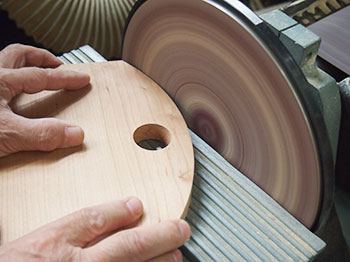
ディスクサンダー等で仕上げ、
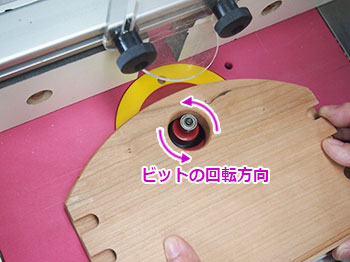
丸面ビットでエッジを面取りします。
エッジの外側と内側では材料の送り方向が異なることに注意が必要です。
いずれもビットの回転方向と対向するように材料を送ります。
少しずつビットを上げて慎重にカットします。
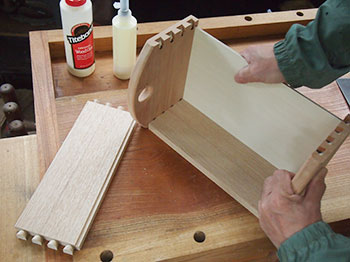
ペーパーで仕上げたら、接着剤を塗布してクランプ。
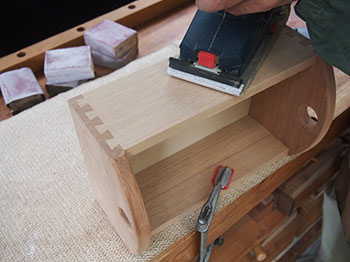
接着剤硬化後にクランプを外し、ジョイント部をフラットにサンディングし、オイルフィニッシュで仕上げ。
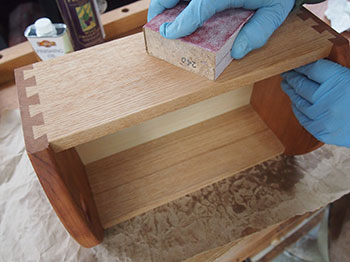
完成した幅の異なる板を使った箱。以前作った短めの箱と一緒に。